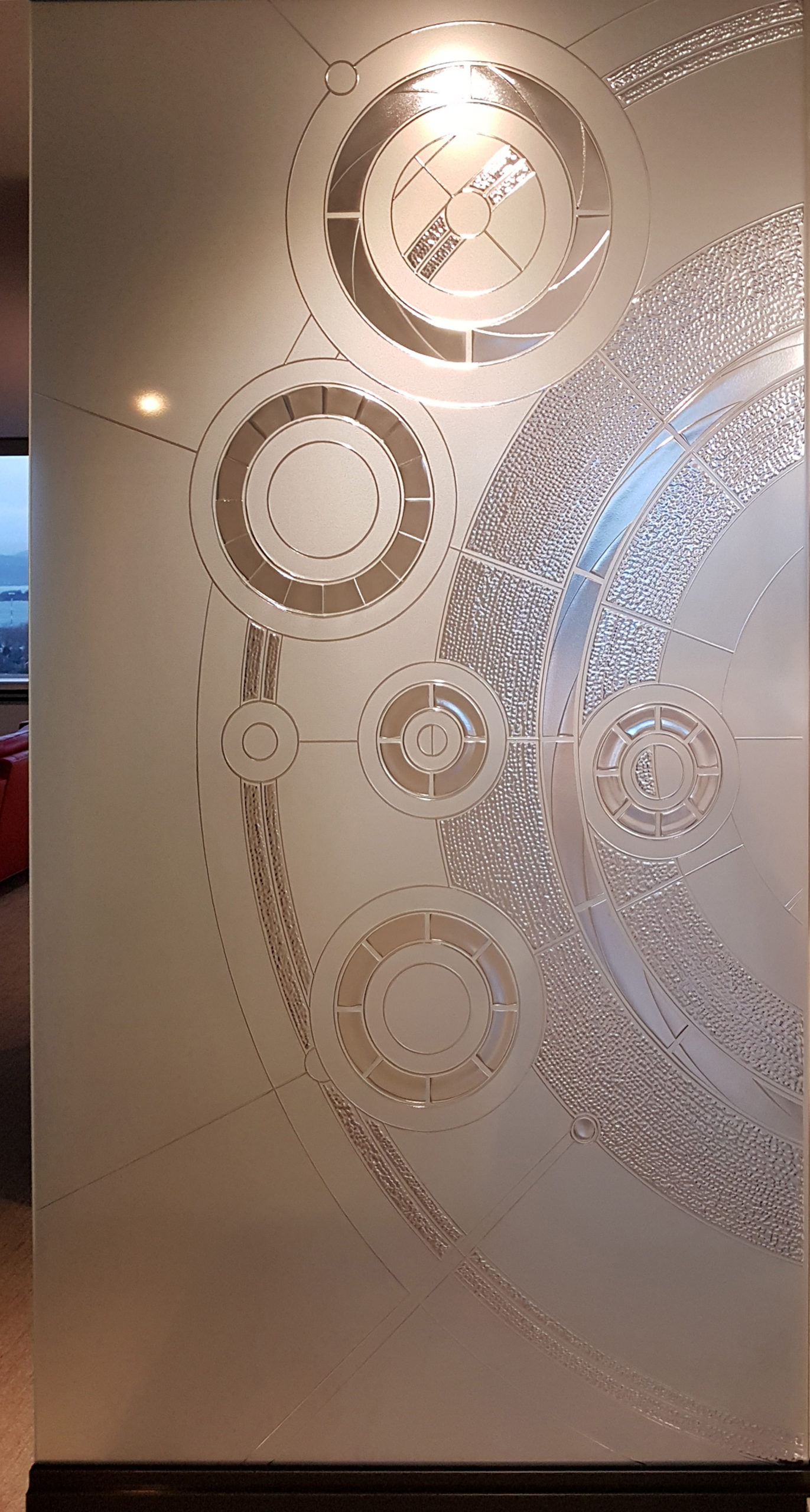
Completed panel installed in custom fabricated base, and upper shoes.
B-u-u-u-u-t-t … this wasn’t a one shot deal…
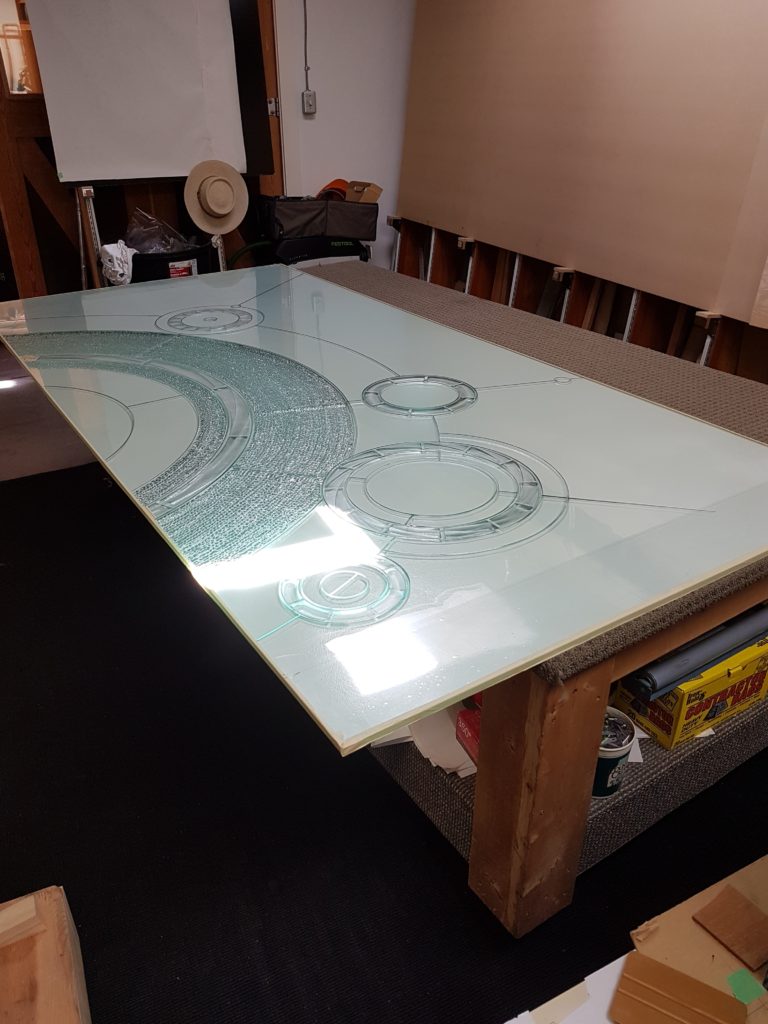
All looks good with the first carved panel, post hi-fire, so it gets masked and the second blast is done – ready for second firing…. But then…
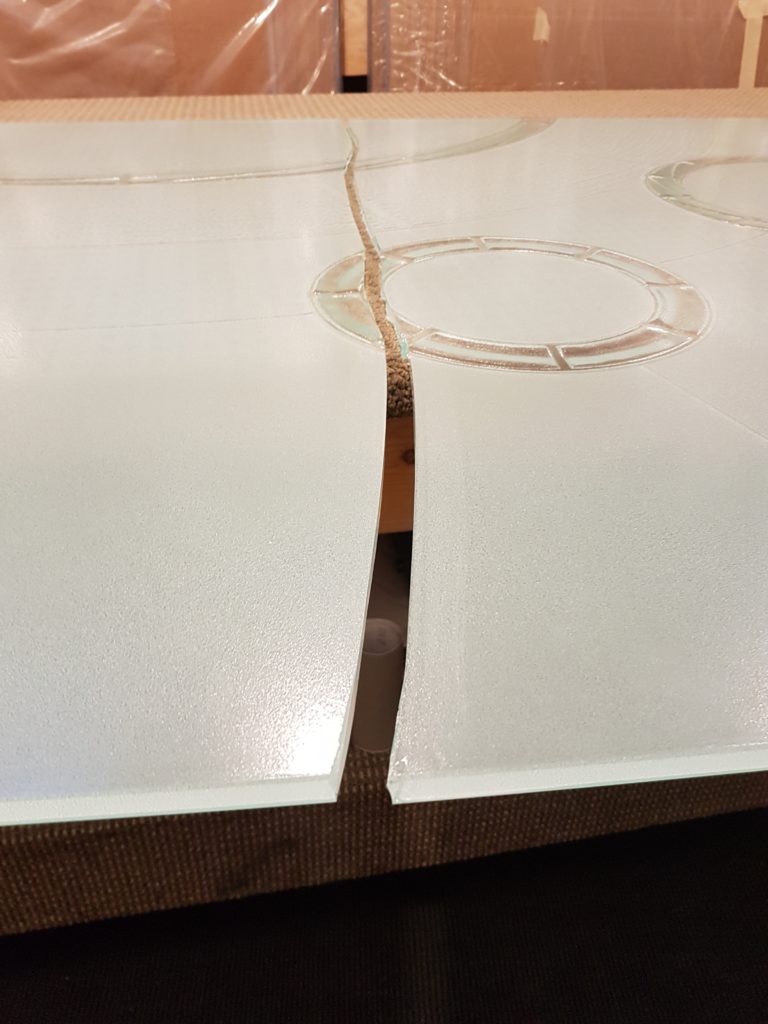
Kracken-a-lacken…!! Dang… Ok well, start over from scratch and assume we just had a bad piece of glass…but nope!
Made an entire second piece – fired it. did the secondary (background) frost) and…
Ka–BanGalang…!! It happened again…! Weeks of work down the tube. And no solution, yet.
Well, meanwhile back at the growing failure pile – a handful of lemons in the shape of four large ‘halves’ of broken dream, got transformed with a willing water jet, some imaginative clients, and a tight welder, into custom ‘lemonade’ furniture…!
A solution for the divider was still being figured out…..
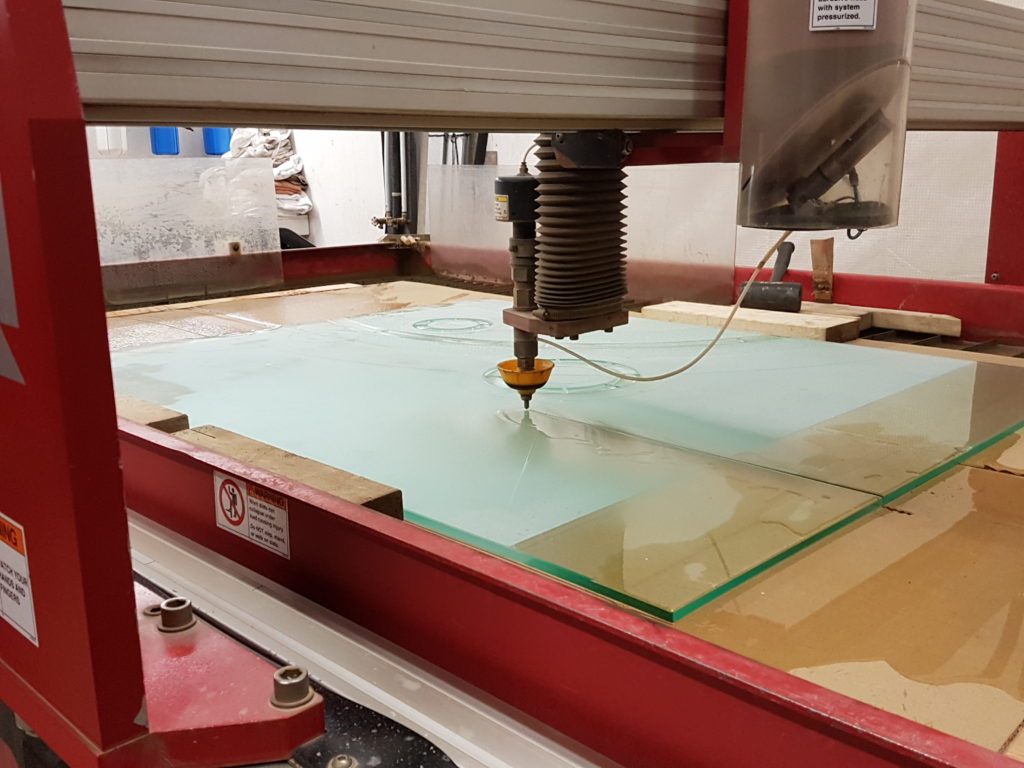
(Waterjet in action)
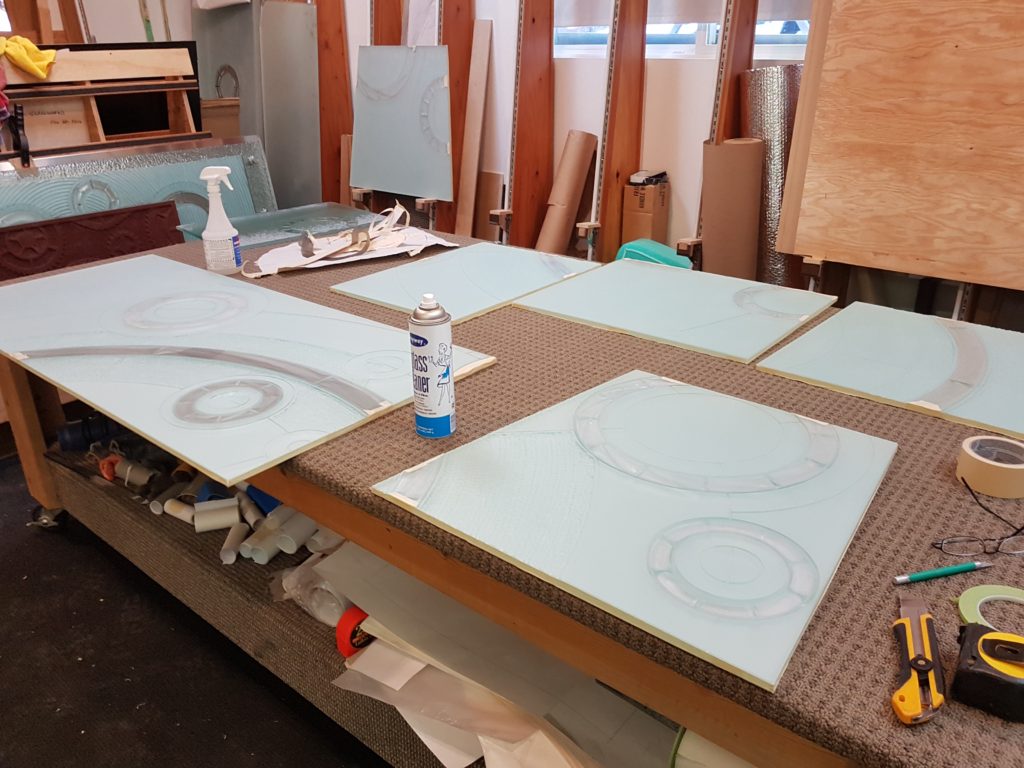
The cut glass receives a re-do of the second blast, and then a firing to “seal” the blast and cut edges.
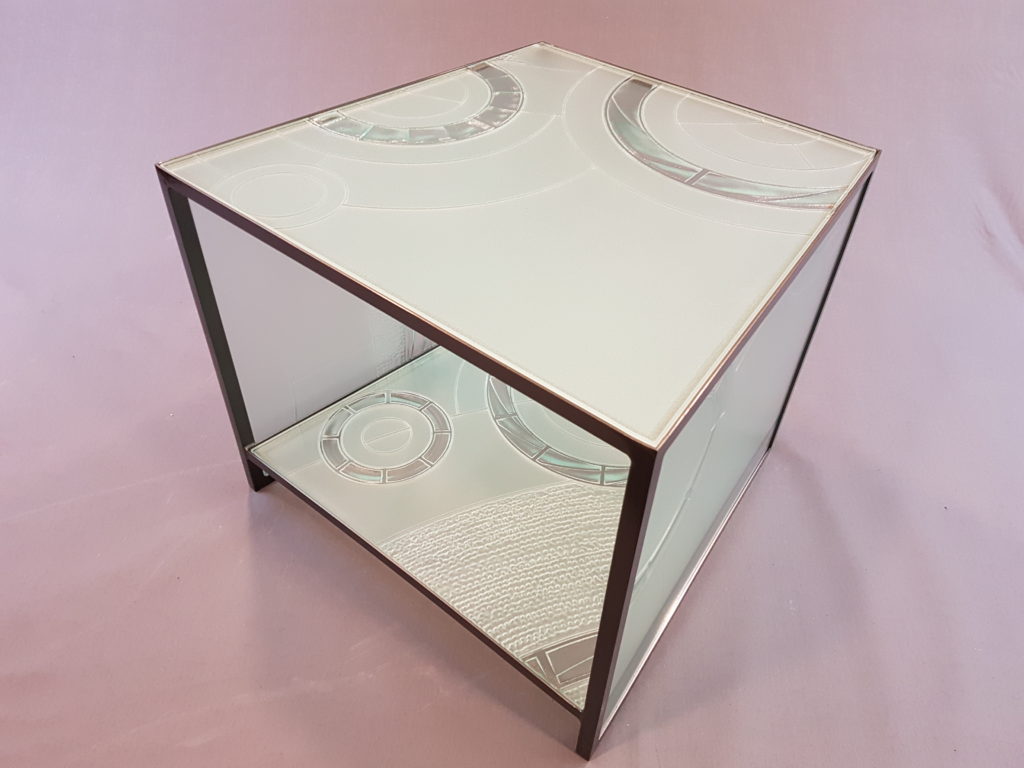
Trapezoidal End Table.
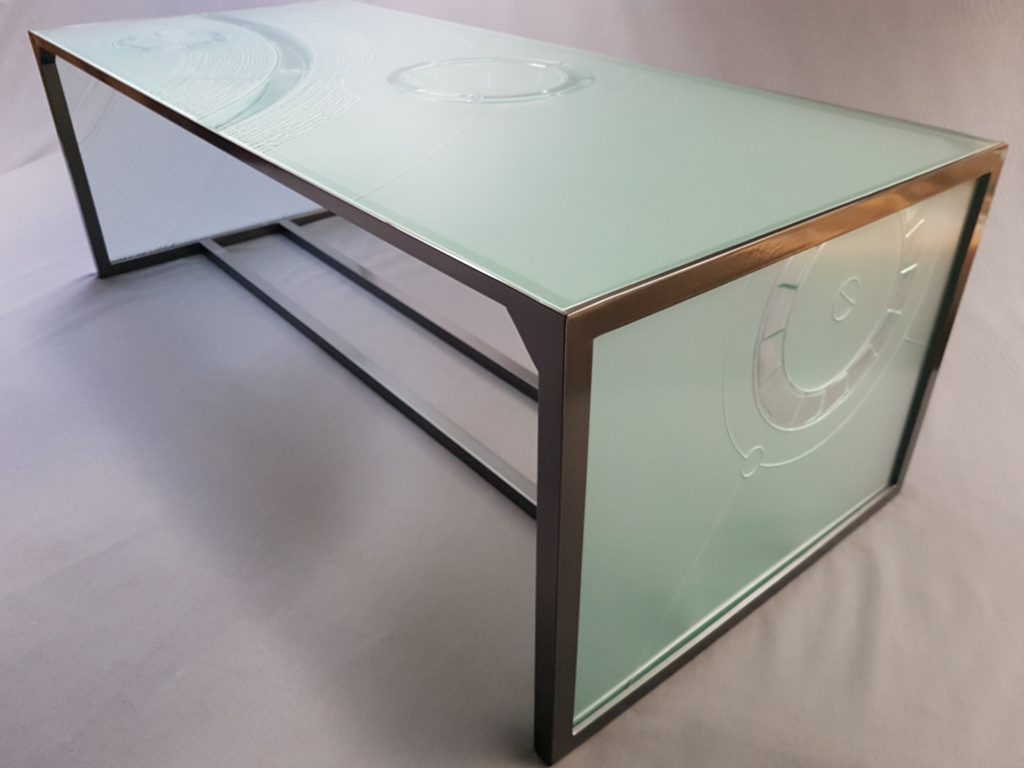
Rectanglizoidal (?) Coffee Table.
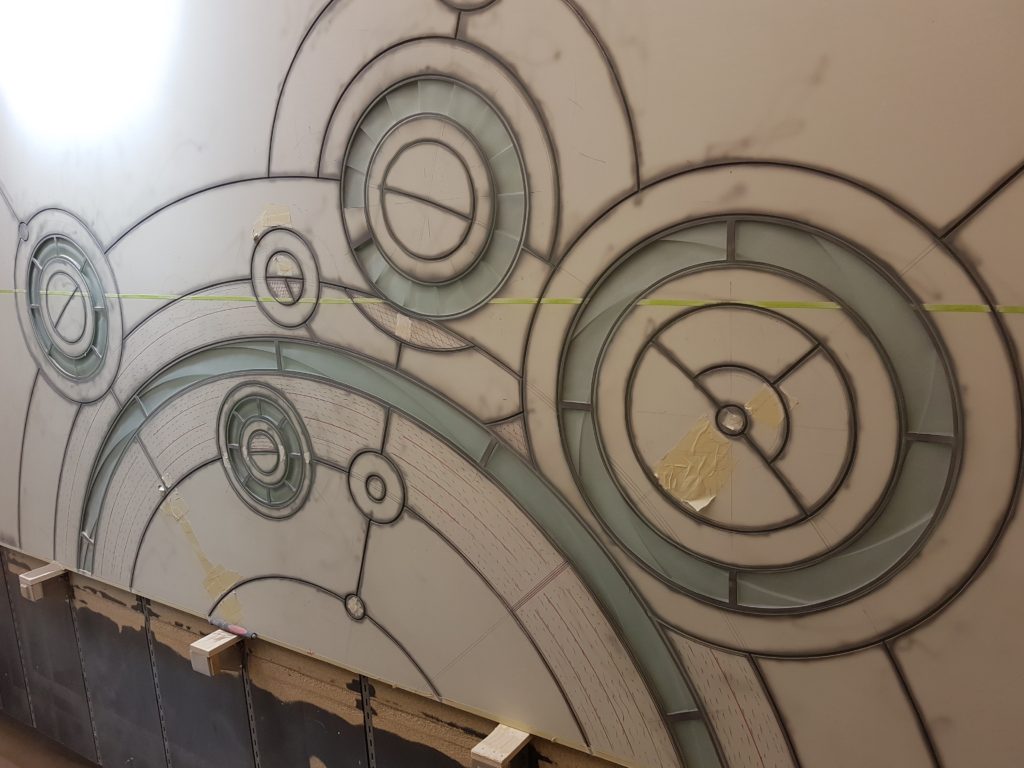
The final attempt at the carving using Fritted Glass. Aha!
This will be fired, and then tempered. And it will stay in one single unbroken piece, get installed, and we will all live happily ever after.
The End.
A TABLE SET FOR TWO
For this project, I was commissioned to create a site/client specific art-glass divider for an apartment undergoing a top to bottom renovation. I met with the clients, the builder, and interior designer Sandy Nygaard, eventually setting upon a course towards “A Table Set For Two”. The apartment reno was going to take a few months, at least. How much of a saga could this project possibly become (hehe)?
After a couple of weeks of carving and firing, the first attempt cracked before it even made it to tempering. Dang! And then so did the second. UGH! Although we’d had success with this process many times before, it seemed that this one had reached some sort of limit regarding tensions created in the glass surface while trying to etch the background specific to a panel of this size… so, it was literally back to the drawing board…
Necessity being the mother of all mother-#@%ing things new and good, I tried something we hadn’t exactly done before – starting with fritted glass. There was a little learn to the heating curve (natch!), but turns out – it turned out. Really great, in fact… (IMHO)!
Working with fritted material was the answer (not an easy or straightforward answer – but definitely the answer…!). I think the end result actually upstaged the original effect I had been chasing in the beginning. Its been outcomes/solutions such as this that have serendipitously steered the direction of this crazy pursuit, as often as not.
The clients – being the best (enablers) in the whole world – went along for the ride and even wanted to utilize the broken bits, if possible…
So, using a modelling program, I made some cut patterns that I could map over the broken chunks, designed table frames, had the broken slabs shaped to size on a local waterjet, and had a very skilled welder work his metal magic, providing a pair of one-off tables for the (now completely renovated) apartment. Thanks to Sandy and the amazing clients for their patience, understanding, and vision (I’ll drink a lemonade to that!).
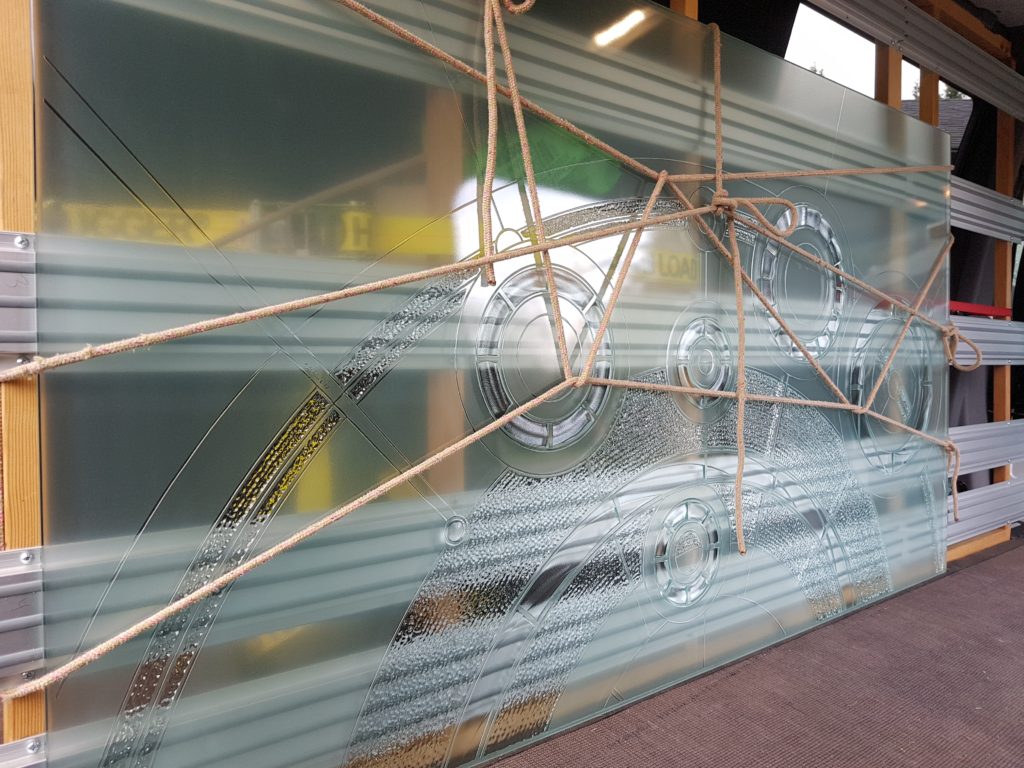
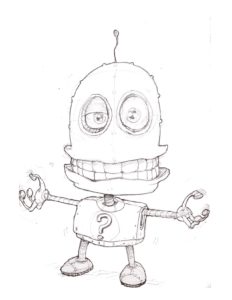
Very nice Charles. V & R … @ YVR